Lockout/Tagout Procedures: Scissor Lift Safety Procedures
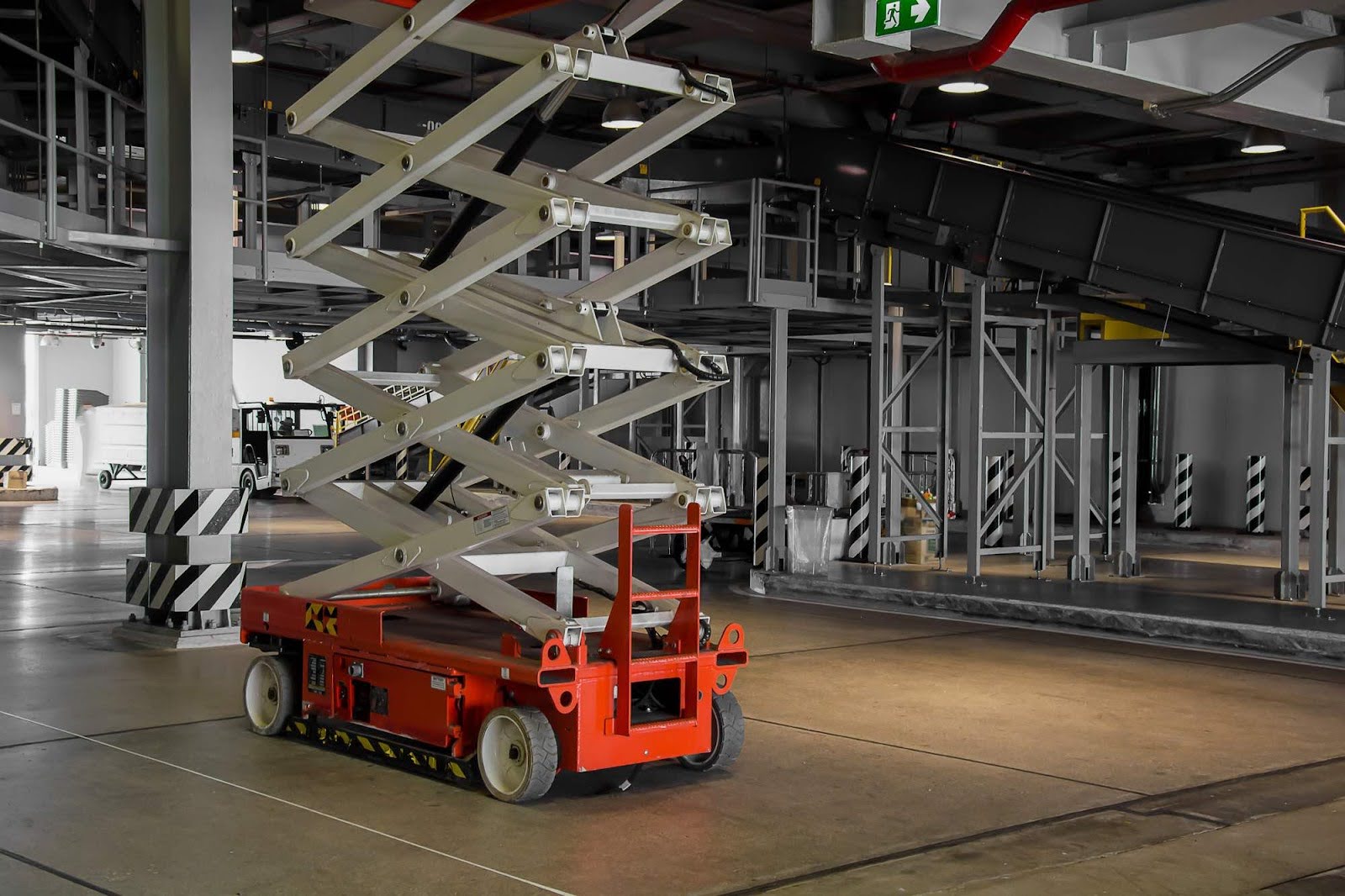
Staying safe while performing maintenance on machinery like a scissor lift should always be a priority. Accidents like hydraulic surges, electrical jolts, or even an accidental lift operation, while a colleague is working underneath the machine are just some of the accidents that can happen if a system isn’t in place to keep workers safe. That’s why implementing a procedure like LOTO (Lockout/Tagout) is critical.
The Preparation
Preparation is essential to successfully implement any system or process. Educate your team so every member involved in LOTO procedures understands the risk and their specific role in protecting equipment and personnel. Assemble proper tools, including locks, tags, and personal protective equipment (PPE), and have clear signage. All of these things form an essential part of the preparation process. The other critical piece is effective communication. Notify all individuals impacted by the LOTO process and ensure you have complete comprehension and cooperation.
Implementing LOTO Effectively
The actual implementation of LOTO involves several steps. You need a firm foundation for any task, so start by stabilizing and securing the base. Next, identify the energy sources – this is a critical step. Workers must then locate and label all potential energy sources, including electricity, hydraulics, and pneumatics, and deactivate and isolate them using designed isolation points. Then, apply dedicated locks and personalized tags to each shut-off device and provide clear warnings. Finally, conduct a thorough check to isolate all energy sources before proceeding.
Scissor Lift Safety
Even while using LOTO, working safely on the scissor lift requires constant vigilance. Workers must remain aware of potential hazards, like falling objects or unplanned equipment activation, and adhere to the established entry and exit protocols to minimize risks. While anyone is working on the lift, keeping communication channels open is critical to ensure everyone’s safety. You must maintain clear dialogue with colleagues on the ground and any other maintenance participants.
In conjunction with these safety measures, using tools like TireSocks’ SafetyPads® can further enhance scissor lift safety. SafetyPads® provide a visible and effective barrier at entry points on construction equipment, clearly marking them with OSHA-compliant black and yellow markings. This heightened visibility reduces the risk of unplanned equipment activation and helps workers maintain constant vigilance.
Reviving the Lift
Reviving the lift post-maintenance is a careful and deliberate process. This step is critical to ensure the safe and effective resumption of equipment functionality. The procedure involves the careful and deliberate actions of the authorized individual who originally applied the Lockout/Tagout (LOTO) procedure. They must systematically remove locks and tags, and then cautiously and methodically reconnect energy sources. This process requires a thorough verification and check of all components to confirm that everything is in proper working order. Once these steps are completed and the lift is deemed safe, it is considered ready for operation.
Lockout/Tagout is more than just a technical procedure; it’s a cultural commitment to safety. By adopting these crucial steps and focusing on proper training, clear communication, and constant vigilance, every scissor lift maintenance task can be conducted with the highest safety standards in mind.
At TireSocks, we are committed to creating a safe, secure, clean environment in every workspace, regardless of height. Contact us today to learn more about how we can help you optimize safety protocols on scissor lifts and other construction equipment.